Electronic Hammer Technology
The driver that operates the electronic hammer is typically installed inside the electrical panel. It creates and transmits electrical signals for more effective operation of the electronic hammer and operates the electronic hammer with various safety devices.
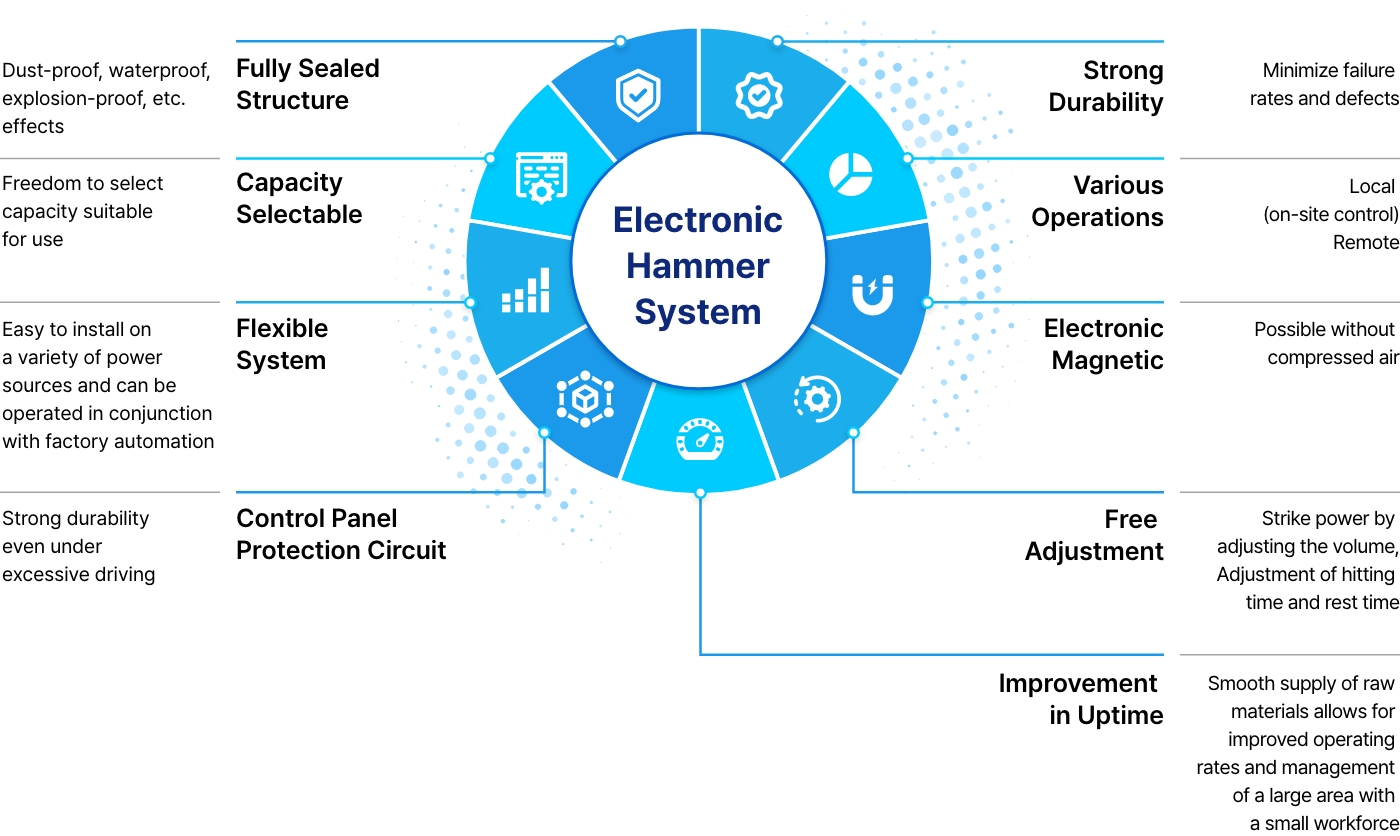
Electronic Hammer System Technology
Function
- On-site control and remote control operation
- Multiple electronic hammers controlled
by a single controller
Electronic Hammer Excellence
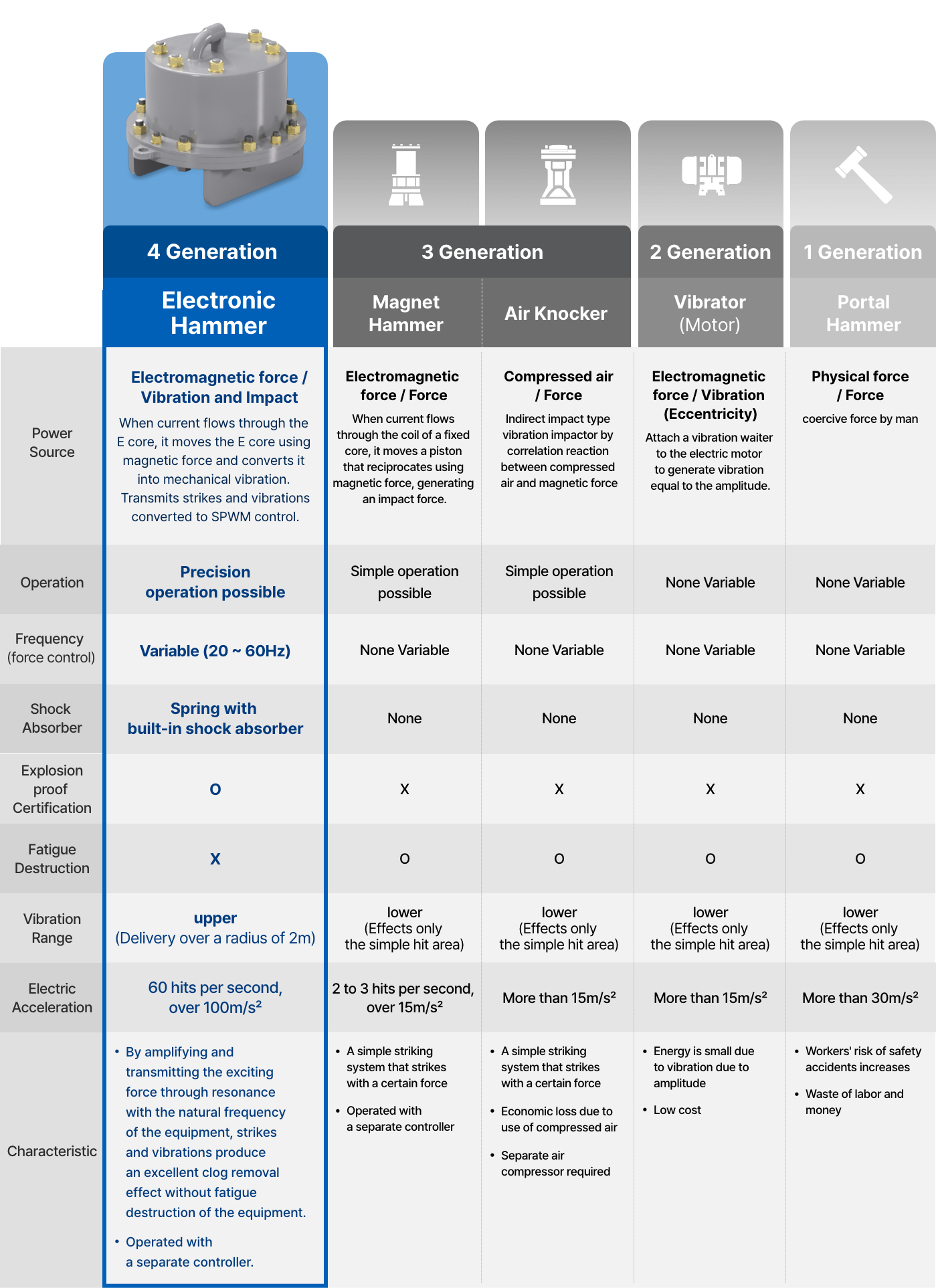
Electronic Hammer Solutions
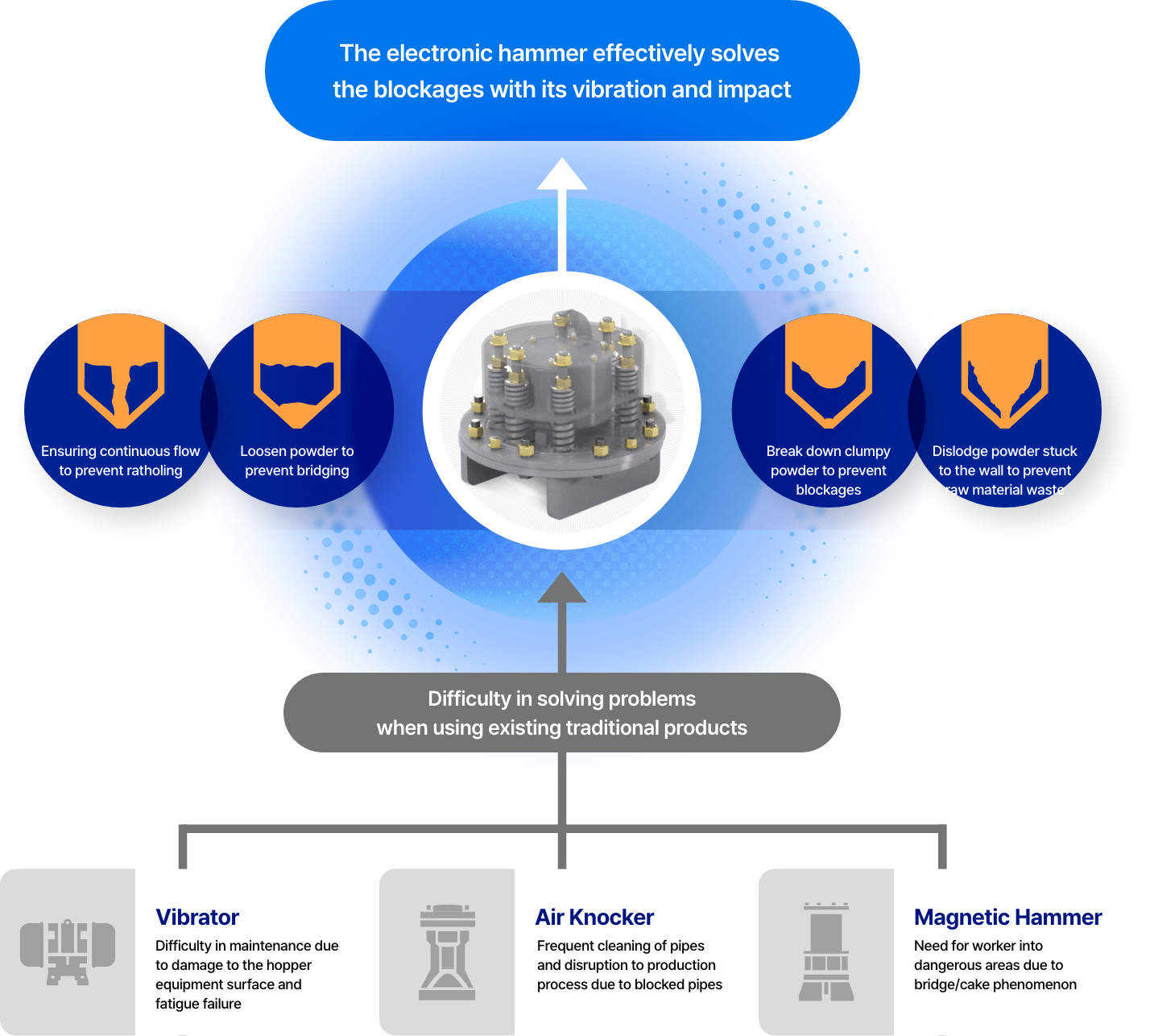
Electronic Hammer Features
System Principles
-
Electromagnetic Force Generation
When alternating current flows through the wire wound around the E-core, electromagnetic force is generated between the E-Core and I-Core by electromagnetic principles
-
Mechanical Vibration Generation
Mechanical vibration and impact occur through the restoring force of elastic springs against electromagnetic force
-
Vibration Radius
Delivers and amplifies momentary powerful impact and vibration to equipment surfaces, transmitting force to inner walls to prevent powder deposits and caking
Specification Selection Criteria
Equipment Proportional Conditions
Models and quantities are selected based on diameter (D) and hopper plate thickness (T), with a hopper angle of repose of 60°. However, these may vary depending on hopper shape, powder properties, and conditions.
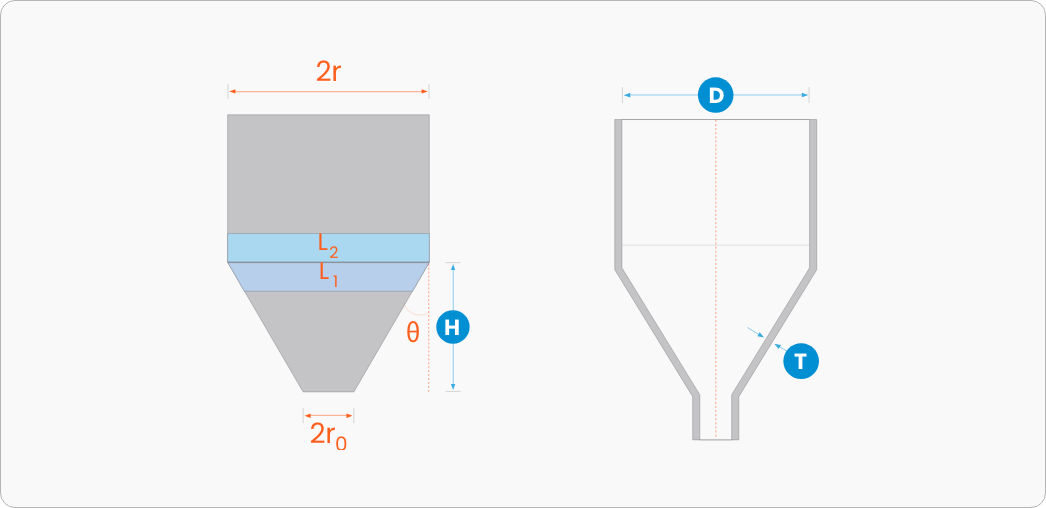
Installation
Quantity
Conditions
The chart below is based on 10mm thickness (T) and does not consider 2ro and L1, L2.
The number of hammer installations may vary depending on circumstances.
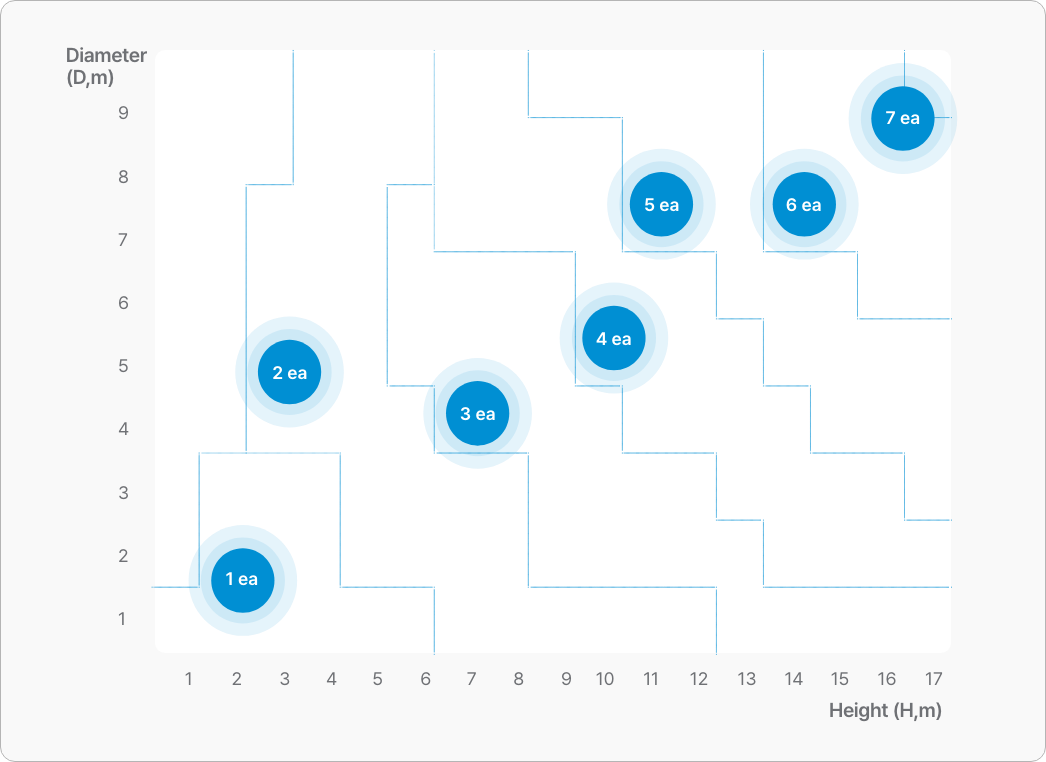